Factory Wastewater & Sewage Treatment Energy-Saving Technology: Spiral Plate Heat Exchanger
Current Challenges
-
Direct Discharge of High-Temperature Wastewater, resulting in severe heat loss
-
High Energy Consumption in wastewater treatment equipment (e.g., heating, aeration, sludge dewatering)
-
Frequent Maintenance of Traditional Heat Exchangers due to scaling and fouling
Improvement Strategies
-
Implement Spiral Plate Heat Exchangers for heat recovery
-
Lower Wastewater Discharge Temperature to reduce thermal pollution
-
Enhance Energy Efficiency, reducing fuel and electricity consumption
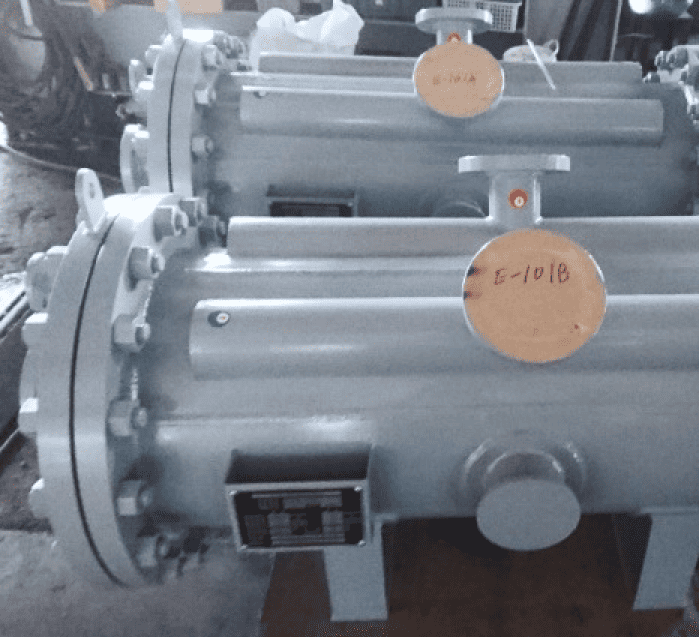
Spiral Plate Heat Exchanger
-
Applications
1. Heat Exchange Between High-Temperature Wastewater & Cold Inlet Water (Enhancing Energy Recovery Efficiency)
2. Heat Exchange in Sludge Treatment Systems (Improving Dewatering Efficiency)
3. Waste Heat Recovery from Wastewater in Chemical & Pulp/Paper Industries (Reducing Heat Loss)
-
Advantages
✅ High Thermal Conductivity (Efficient heat transfer through internal evaporation & condensation in heat pipes)
✅ Turbulent Flow Effect Reduces Scaling, ideal for high-pollution water treatment
✅ Efficient Heat Exchange, maximizing waste heat utilization
✅ Compact Design, suitable for limited installation spaces
✅ Compatible with Corrosive Fluids, with optional anti-corrosion materials