High-Efficiency Energy-Saving Technologies for Steel Plants: Applications of Heat Pipe and Spiral Plate Heat Exchangers
Current Challenges
-
High-Temperature Flue Gas Emissions (e.g., blast furnaces, converters, reheating furnaces)
-
Low Efficiency of Traditional Heat Exchangers (Poor heat transfer, rapid fouling)
-
Frequent Maintenance (Affecting production efficiency)
Improvement Strategies
-
Install Heat Pipe & Spiral Plate Heat Exchangers to enhance waste heat recovery
-
Reduce Maintenance Costs and extend equipment lifespan
-
Lower Fuel Consumption and reduce chimney emissions

Heat Pipe Heat Exchanger
-
Applications
1. Blast Furnace Hot Stoves – Recovering flue gas heat to preheat combustion air
2. Sinter Plant Exhaust Gas Recovery – Reducing exhaust temperature and improving energy recovery efficiency
3. Converter Flue Gas Cooling – Lowering emission temperature and recovering waste heat
-
Advantages
✅ High Thermal Conductivity (Heat transfer through internal evaporation & condensation)
✅ Adaptable to High-Temperature Environments
✅ Modular Design, allowing individual tube replacement for easy maintenance
✅ Minimizes Ash Buildup & Corrosion, improving long-term efficiency
-
Case Study: The blast furnace exhaust recovery system
1. Installed a heat pipe heat exchanger in the blast furnace exhaust system to recover 300°C waste gas heat.
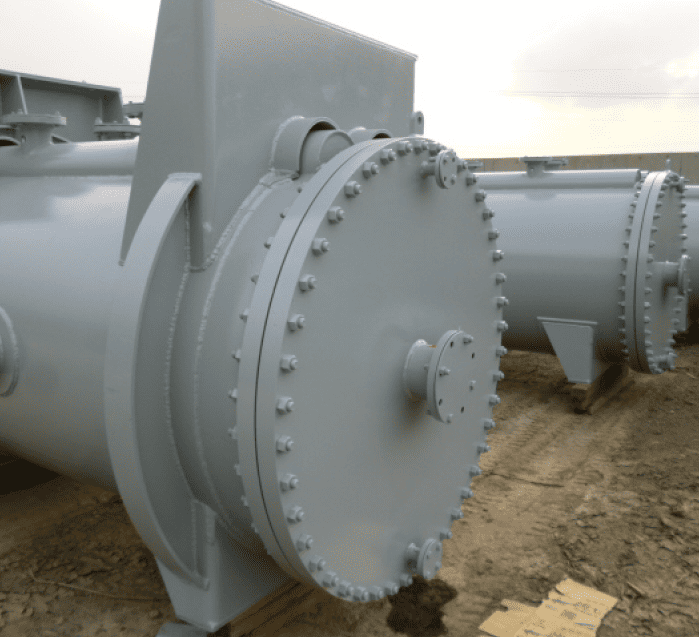
Spiral Plate Heat Exchanger
-
Applications
1. High-Temperature Water Cooling Systems – Minimizing cooling water usage
2. High-Temperature Water Cooling Systems – Minimizing cooling water usage
3. Hydraulic Cooling System in Steel Plate Press machine (improve cooling efficiency)
-
Advantages
✅ High Thermal Conductivity (Heat transfer through internal evaporation & condensation)
✅ 30–50% Higher Heat Exchange Efficiency (Turbulent flow effect from spiral design)
✅ Reduced Fouling, lowering maintenance requirements
✅ Compact Design, suitable for tight installation spaces
✅ Capable of High-Temperature & High-Pressure Applications (Up to 4 MPa)
-
Case Study: High-Temperature Steam Condenser Upgrade with Spiral Plate Heat Exchanger