High-Efficiency Energy-Saving Technologies for Pharmaceutical & Food Factories: Applications of Heat Pipe and Spiral Plate Heat Exchangers
Current Challenges
-
High Consumption of Steam and Hot Water (e.g., sterilization, drying, pasteurization, boiling)
-
Direct Emission of High-Temperature Exhaust Gas, resulting in significant heat loss (e.g., boilers, drying equipment)
-
Rapid Scaling of Traditional Heat Exchangers, leading to frequent maintenance and affecting production stability
Improvement Strategies
-
Install Heat Pipe Heat Exchangers & Spiral Plate Heat Exchangers to enhance heat recovery efficiency
-
Install Heat Pipe Heat Exchangers & Spiral Plate Heat Exchangers to enhance heat recovery efficiency
-
Decrease Heat Exchanger Maintenance Frequency to improve equipment uptime
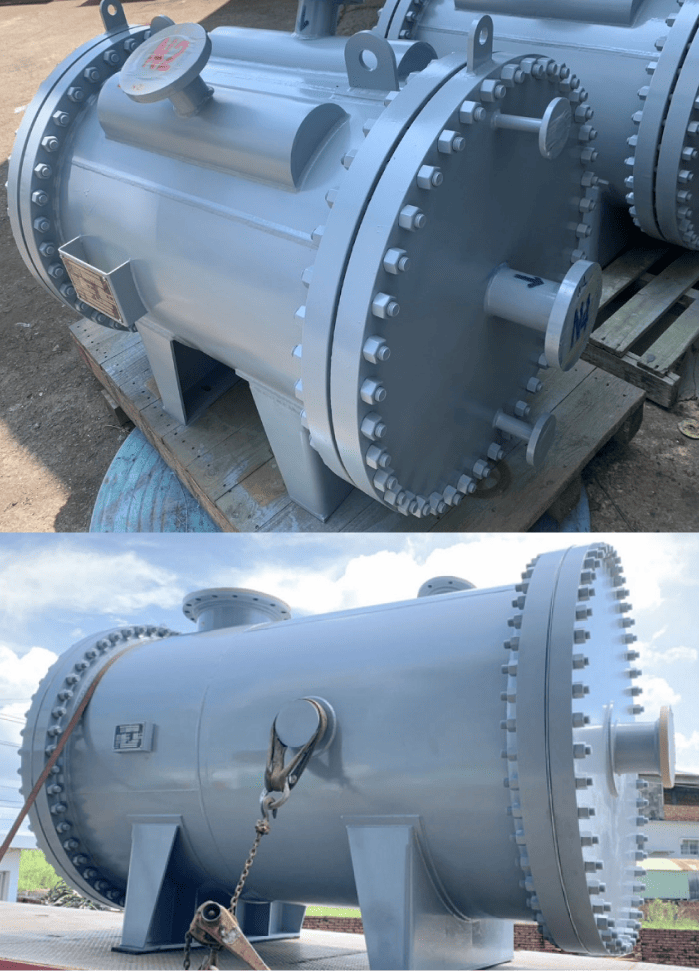
Spiral Plate Heat Exchanger
-
Applications
1. Pharmaceutical Factories: Steam Condensate System
2. Food Processing Plants: Waste Heat Recovery from Pasteurization / Cooking Systems
3. Steam Condensate Recovery
-
Advantages
✅ High Thermal Conductivity (Heat transfer through internal evaporation & condensation)
✅ Increase in Heat Exchange Efficiency (Enhanced turbulence from spiral flow)
✅ Self-Cleaning Design: Reduces fouling and clogging
✅ Compact Size: Suitable for limited installation spaces
✅ Food-Grade & Sterile Applications: Optional stainless steel material for hygiene compliance