Biotech & Biomass Factory Energy-Saving Technology: Applications of Heat Pipe & Spiral Plate Heat Exchangers
Current Challenges
-
Direct Discharge of High-Temperature Exhaust Gas & Steam, causing severe heat loss
-
High Energy Consumption in processes like fermentation, sterilization, and drying
-
Traditional Heat Exchangers Prone to Scaling, reducing efficiency and requiring frequent maintenance
Improvement Strategies
-
Install Heat Pipe & Spiral Plate Heat Exchangers to enhance waste heat recovery
-
Reduce Fuel & Steam Consumption, lowering production costs
-
Minimize Heat Exchanger Maintenance Needs, improving equipment uptime
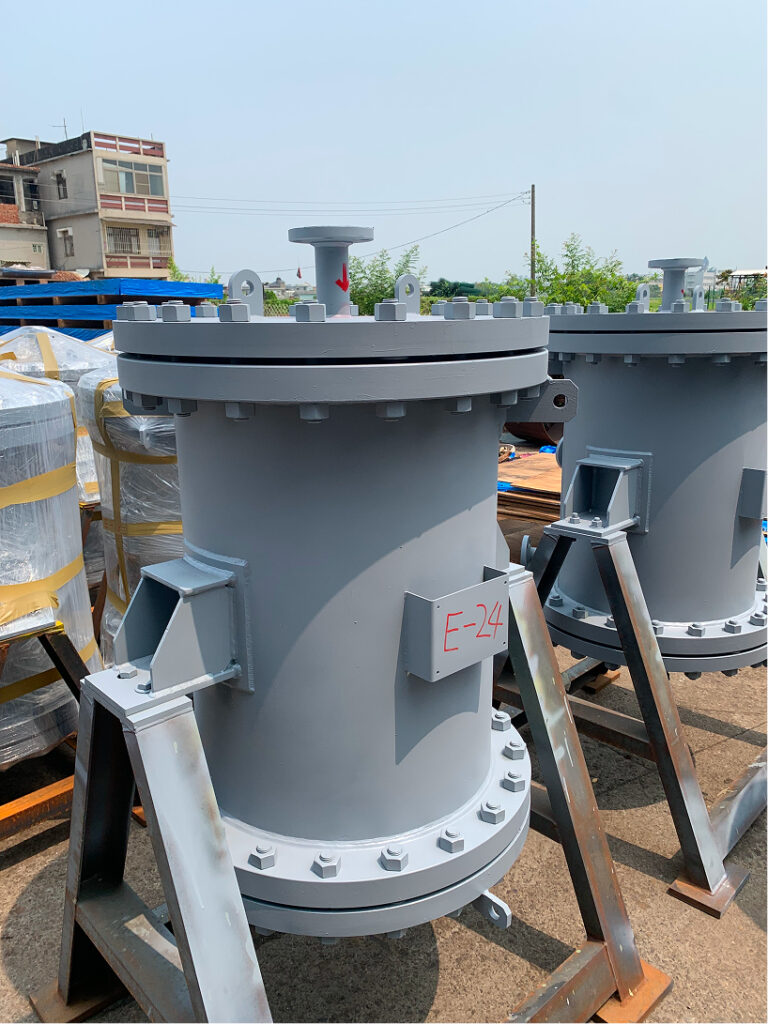
Spiral Plate Heat Exchanger
-
Applications
1. High temperature steam condensation (reducing steam loss)
2. Process heating/cooling (such as hot oil/water cooling)
3. Sewage / high viscosity fluid heat exchange (good self-cleaning effect)
-
Advantages
✅ High efficiency heat exchange, improving steam and hot water recovery efficiency
✅ High efficiency heat exchange, improving steam and hot water recovery efficiency
✅ Compact Size: Suitable for limited installation spaces
✅ Suitable for corrosive fluids, stainless steel or anti-corrosion materials available